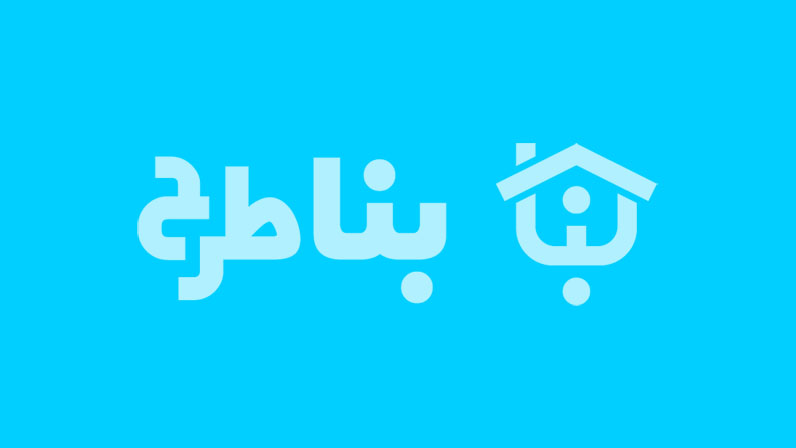
17-14 جوشکاری (بخش دوم لولهکشی گاز طبیعی با فشار 2 الی 60 پوند بر اینچ مربع)
17-14-1 جوشکاری شبکههای گازرسانی فولادی
17-14-1-1 کلیات
جوشکاری لولههای فولادی گاز و اتصالات مخصوص آنها باید به روش جوشکاری برقی دستی انجام شود. روش جوشکاری دستی، بازرسیها و کیفیت آن باید مطابق استاندارد API -1104 باشد.
17-14-1-2 ارزیابی و تعیین صلاحیت جوشکاران
جوشکارانی که برای جوشکاری لولههای فولادی گاز به کار گرفته میشوند باید قبل از اقدام به جوشکاری بر طبق روش جوشکاری تأیید شده و بر اساس استاندارد API-1104 مورد ارزیابی قرار گیرند.
در صورت قبولی باید به هر جوشکار یک شماره به عنوان کد جوشکار اختصاص داده شود.
در صورت تغییر در روش جوشکاری، ارزیابی جوشکاران باید مجدداً و بر طبق روش جدید انجام شود.
مسئولیت کنترل مدارک، صلاحیت، ارزیابی جوشکاران و بررسی و تائید روش جوش بر عهده دستگاه نظارت است. در صورت لزوم دستگاه نظارت میتواند برای ارزیابی جوشکاران از موسسات و شرکتهای ذیصلاح استفاده نماید، ولی در هر صورت مسئولیت به عهده دستگاه نظارت است.
17-14-1-3 الکترودهای جوشکاری
برای جوشکاری لولههای گاز باید در پاس اول جوش از الکترودهای مطابق با استاندارد AWS-E6010 و در پاس دوم و پاسهای بعدی جوش از الکترودهای مطابق با استاندارد AWS-E6010 و یا AWS-E7010 استفاده شود.
قبل از استفاده از الکترودهای جوشکاری، نمونه آنها باید به وسیله دستگاه نظارت مورد بررسی قرار گیرد. در صورت لزوم دستگاه نظارت باید آزمایشهای مربوطه را انجام داده و نهایتاً کاربرد آن را در جوشکاری شبکههای گاز تأیید نماید.
انتخاب قطر، نوع الکترود و تنظیم آمپر و ولتاژ و سایر پارامترهای جوشکاری باید بر اساس روش جوشکاری تائید شده صورت گیرد.
الکترودهای جوشکاری باید تا زمان استفاده در بستهبندی اولیه خود و بر طبق توصیه سازنده نگهداری شوند. الکترودهائی که جعبه آنها برای مصرف باز میشوند باید تا زمان مصرف برای جلوگیری از جذب رطوبت و صدمه به پوشش در گرمکنهای مخصوص قرار داده شوند.
الکترودهائی که به علت جذب رطوبت، وارد آمدن صدمه به پوشش آنها و یا اشکالاتی از قبیل یکطرفه سوختن، انحراف قوس و ریزش پوشش در حین جوشکاری، برای جوشکاری مناسب نباشند، باید به وسیله دستگاه نظارت بررسی و از کارگاه خارج شوند.
17-14-1-4 آمادهسازی لولههای فولادی قبل از عملیات جوشکاری
لولههای فولادی قبل از جوشکاری باید مورد بازرسی قرار گیرد و در صورت مشاهده عیوب مکانیکی از قبیل شیار، فرورفتگی، خراش و دوپهنی، وارد آمدن صدمه به سر لوله و حفرههای خوردگی، باید کنار گذارده شوند. قبل از جفت کردن لولهها و شروع عملیات جوشکاری باید سر لولهها بصورت دور تا دور و به فاصله یک سانتیمتر با استفاده از برس برقی تمیز و براق گردد. در صورت نیاز به برش و پخ زدن سر لولهها، این کار باید به نحوی انجام گیرد که مقطع بریده شده، عمود بر محور طولی لوله باشد. حداکثر میزان انحراف صفحه برش لوله از حالت عمود بر محور طولی لوله برابر با 1/5 میلیمتر است.
17-14-1-5 کنترلهای لازم قبل از شروع جوشکاری
قبل از شروع جوشکاری موارد زیر باید به وسیله دستگاه نظارت کنترل گردد:
1- لبه لولهها، قسمت عمودی لبه لوله و حدود یک سانتیمتر از سر لوله به صورت دور تا دور از نظر زاویه، پخ و تمیز و براق بودن پخ.
2- در صورت برش لوله با دستگاه لوله بر، باید پلیسههای داخلی لوله کاملأ به وسیله سوهان برداشته و لبه لوله بر طبق روش جوشکاری تأیید شده پخ زنی شود.
3- در صورت برش و پخ زنی لوله با دستگاههای مخصوص این کار، باید پخ سر لوله بر طبق روش جوشکاری تأیید شده با سوهانکاری آمادهسازی شود. ضمناً باید کنترل شود که صفحه برش، عمود بر محور طولی لوله و یا در حد رواداری مجاز آن باشد.
4- با عبور دادن یک صفحه مدور متناسب با قطر داخلی لوله، از داخل لوله، ضمن کنترل سلامت قطر لوله، از عدم وجود اشیاء باقی مانده داخل لوله، باید اطمینان حاصل نمود.
17-14-1-6 اقدامات لازم قبل از جوشکاری لولهها
الف- پیش گرمی لبه لولهها – تعیین مناسب بودن شرایط جوی برای عملیات جوشکاری بر عهده دستگاه نظارت است. در ساعات اولیه صبح و یا در شرایطی که دمای محیط کمتر از 5+ درجه سانتیگراد باشد، پیشگرمی لولهها حداقل تا دمای50+ درجه سانتیگراد الزامی است.
ب- جفت کردن لولهها – جفت کردن لولهها باید به وسیله کلمپها یا گیرههای همترازی خارجی که قادر باشند سر لولهها را به صورت ثابت نگهداشته و انجام جوشکاری در زیر آنها امکانپذیر باشد، صورت گیرد. کلمپ یا گیره همطرازی باید به گونهای باشد باشد که حداقل امکان جوشکاری 50% محیط لوله در ربعهای متقابل در زیر آن امکانپذیر باشد. مناسب بودن و کارائی گیره همترازی باید به وسیله دستگاه نظارت مورد تأیید قرار گیرد.
برای جفت کردن و همتراز کردن لولهها استفاده از چکش فولادی مجاز نمیباشد. در صورت لزوم تنها استفاده از چکشهای برنجی مجاز میباشد.
لولههای گاز باید به طریقی همتراز شوند که جوش طولی آنها حدالامکان در موقعیت ساعات 10 و 2 قرار گیرند. جوشکاری لولهها در شرایطی که جوش طولی آنها در یک راستا قرار گیرد مجاز نمیباشد.
برای تسهیل و ایمنی در جوشکاری باید لولهها را در ارتفاع مناسبی از سطح زمین بر روی پایههائی که به تعداد و ارتفاع لازم تهیه شده باشند انجام داد. پایههای مربوطه باید دارای بالشتکهای نرم باشند تا از وارد آمدن صدمه به پوشش لولهها جلوگیری نمایند.
17-14-1-7 جوشکاری شبکههای گازرسانی فولادی
هر گونه عملیات جوشکاری باید براساس روش تأیید شده صورت گیرد.
قبل از اقدام به هر گونه عملیات جوشکاری باید از طرف مجری، روش جوشکاری تهیه و جهت بررسی به دستگاه نظارت ارائه گردد. دستگاه نظارت باید پس از انجام اصلاحات روش را مورد تایید قرار دهد.
دستگاه نظارت میتواند برای این منظور از خدمات موسسات و شرکتهای ذیصلاح استفاده نماید که در این صورت مسئولیت بر عهده آن شرکتها خواهد بود.
الف- جوشکاری پاس یک
1- جوشکاری در زیر گیره همترازی جوشکاری در زیر گیره همترازی باید حداقل معادل با 50% محیط لوله و در ربعهای متقابل و به روش سرازیر انجام گردد. در خصوص لوله 2 اینچ، جوشکاری در ربعهای متقابل کافی میباشد.
استفاده از خال جوش مجاز نبوده و حداقل طول قابل قبول برای جوش سه سانتیمتر میباشد.
در صورتی که قطر لوله 10 اینچ و بالاتر باشد جوشکاری کلیه پاسها باید به وسیله دو جوشکار به صورت همزمان انجام شود.
2- تکمیل جوشکاری پاس یک
پس از باز کردن گیره همترازی باید قسمتهای پایانی جوش در هر قسمت را با دستگاه سنگ سنباده برقی تمیز کرده و سپس نسبت به جوشکاری قسمتهای باقیمانده به روش سرازیر اقدام نمود.
ب- جوشکاری پاس دو
پس از تکمیل پاس یک جوش باید با استفاده از دستگاه سنگ سنباده برقی اقدام به سنگ زنی پاس یک نمود تا قسمتهای برآمده و غیریکنواخت جوش و عیوب آن برداشته شود. سپس باید بلافاصله و تا قبل از سرد شدن جوش نسبت به جوشکاری پاس دوم جوش به روش سرازیر اقدام نمود.
پ- جوشکاری پاسهای پر کننده و تاج جوش
پس از تکمیل پاس دو جوش باید با استفاده از دستگاه برس برقی اقدام به تمیز کردن پاس دو نمود.
سپس جوشکاری پاسهای پر کننده و تاج جوش به روش سرازیر انجام شود. عرض پاس نهائی باید حداقل به اندازه یک میلیمتر پهنتر از پخ لوله در طرفین جوش بوده و ارتفاع آن نباید بیش از 5/1 میلیمتر بالاتر از سطح لوله باشد.
پس از جوشکاری هر پاس جوش باید سرباره جوش را به طور کامل پاک نمود و در صورت لزوم برآمدگیهای اضافی جوش را سنگزده و یکنواخت نمود. سنگ زدن تاج جوش به هیچ وجه مجاز نمیباشد.
در زمان جوشکاری پاسهای مختلف جوش، نباید اجازه داد که الکترود جوشکاری یا اهرم اتصال زمین آن به قسمتهای دیگر لوله به جز محل پخ آن متصل شده و جرقه بزند. جوشکار باید از برخورد نوک الکترود جوشکاری با بدنه لوله که موجب سوختگی خواهد شد، جلوگیری نماید. در پایان هر روز کاری باید کلیه جوشهای آن روز تکمیل شده باشد.
در پایان هر روز کاری باید با استفاده از درپوش مناسبی سرهای باز لوله را به طریق مطمئنی مسدود کرد تا آب و فاضلاب، خاک، زباله، اجسام خارجی و حیوانات کوچک به داخل لوله وارد نشوند. در صورت استفاده از درپوش فلزی، جوشکاری آن به لوله مجاز نمیباشد.
فاصله دو جوش محیطی برای لولههای با قطر 4 اینچ و کوچکتر باید از 15 سانتیمتر کمتر نباشد و این فاضله برای لولههای با قطر بزرگتر از 4 اینچ حداقل باید یک برابر قطر لوله باشد.
ت- جوشکاری اتصالات نهائی
جوشکاری اتصالات نهائی باید بر طبق روش پیشنهادی مجری و با تأیید دستگاه نظارت انجام شود.
اتصالات نهائی باید با دقت همتراز شوند به طوری که تنشهای حاصله از جوشکاری را به حداقل برساند. برای جفت کردن لولهها ممکن است حفاری قسمتهائی از کانال در دو طرف و تغییر شیب کانال الزامی باشد. در جوشکاری اتصالات نهائی، اجرای خال جوش با رعایت حداقل سه سانتیمتر طول جوش مجاز میباشد.
ث – جوشکاری شیرها، اتصالات و فلنج ها
در جوشکاری شیرها، اتصالات و فلنجها، درصورتی که قطر داخلی آنها با قطر داخلی لوله اختلاف داشته و این اختلاف بیش از 2/5 میلیمتر باشد، باید قطر کوچکتر تا اندازه قطر بزرگتر با نسبت سه به یک سنگزده شود.
در جوشکاری فلنجها باید دقت کافی به عمل آید تا صفحه فلنج بر محور طولی لوله عمود بوده و سوراخهای فلنج با وسیله متصل شونده به آن در یک راستا قرار گیرد. ضمناً برای جلوگیری از بروز نشتی در آینده باید دقت شود تا به محل نشست واشر آسیبی نرسد.
جوشکاری اتصالات به یکدیگر و اتصالات به شیرها بلامانع است ولی بهتر است فاصله دو جوش متوالی حداقل به میزان یک برابر قطر لوله بزرگتر باشد.
در صورت عدم امکان استفاده از گیره همترازی اجرای خال جوش مشروط بر آنکه حدالامکان سه سانتیمتر طول داشته باشد مجاز است.
ج- تعمیر جوش ها
روش تعمیر جوش ها: هر گونه عملیات جوشکاری جهت تعمیر جوشها باید بر اساس روش تأیید شده صورت گیرد.
جهت تعمیر جوشها باید روش جداگانهای از طرف مجری تهیه شده و به وسیله دستگاه نظارت مورد بررسی قرار گرفته و در صورت نیاز پس از انجام اصلاحات لازم مورد تایید قرار گیرد. دستگاه نظارت میتواند برای این منظور از خدمات موسسات و شرکتهای ذیصلاح استفاده نماید، ولی در هر صورت مسئولیت کلی کار بر عهده دستگاه نظارت است.
جهت تعمیرات جوش اعم از آنکه جوشکاری در داخل کانال و یا بیرون از کانال انجام شود، رعایت موارد زیر الزامی است:
1- پیشگرمی لبههای دو طرف جوش حداقل تا دمای 50 درجه سانتیگراد الزامی است.
2- جوشکاری پاس یک جوش به روش سربالا مجاز است.
3- جوشهایی که به علت نتیجه تفسیر فیلمهای رادیوگرافی و یا در نتیجه بازرسی عینی دستگاه نظارت معیوب تشخیص داده شوند باید زیر نظر دستگاه نظارت تعمیر شده و یا در صورت لزوم بریده شوند.
4- جوشهای دارای شیارهای جانبی و تاج جوشهایی که نیاز به تقویت دارند باید زیر نظر دستگاه نظارت تعمیر و تکمیل شوند.
5- در صورت وجود هرگونه ترک در جوش، باید کل جوش بریده شود. ترکهای ستارهای ایجاد شده در نقاط توقف جوشکاری در صورتی که سنگزده شده و از بین بروند بلامانع خواهند بود.
6- قبل از شروع به تعمیر جوش، باید محل عیب از گزارشهای رادیوگرافی استخراج و بر روی جوش مشخص گردد. سپس با استفاده از سنگ سمباده برقی قسمت معیوب بصورت کامل برداشته شود.
7- پس از تعمیر در صورتیکه اشکالی مشاهده نگردد، باید از جوش تعمیر شده رادیوگرافی به عمل آید.
در صورت مشاهده هرگونه عیب غیرقابل قبول در رادیوگرافی از جوش تعمیر شده، جوش باید بریده شود.
8- تعمیرات جوش باید تا قبل از عایقکاری سرجوشها انجام شود. جوشهای تعمیر شده باید با نظر دستگاه نظارت عایقکاری شوند.
چ- تهیه گزارشهای روزانه جوشکاری
در پایان هر روز کاری باید گزارشهای جوشکاری در فرم مخصوص توسط مجری تهیه و جهت بررسی و تأیید به دستگاه نظارت ارائه شود.
گزارش جوشکاری باید حاوی اطلاعات جوشکاریهای انجام شده از جمله قطر و ضخامت لوله، جنس لوله، طول لوله، شماره خطوط، شماره جوش ها،کد جوشکاران و جمع طول لوله جوشکاری شده باشد.
ح- بازرسی جوش
کلیه جوشها باید به وسیله دستگاه نظارت مورد بازرسی عینی قرار گرفته و در صورت معیوب بودن تعمیر یا بریده شود. دستگاه نظارت میتواند در صورت لزوم برای یافتن عیوب سطحی از بازرسی به روش مایعات نفوذ کننده یا ترک یابی مغناطیسی استفاده نماید.
خ- پرتونگاری
کلیه جوشهای لولههای مدفون و غیرمدفون با قطر 2 اینچ و بالاتر باید به صورت صد در صد مورد پرتونگاری قرار گیرند.
پرتونگاری از جوشها باید به وسیله شرکتهای مجاز، معتبر و با سابقه پرتونگاری انجام شود. انتخاب شرکت مجری پرتونگاری باید به وسیله مجری بررسی و با تایید دستگاه نظارت انجام شود.
پرتونگاری باید بر اساس روشی که به وسیله شرکت پرتونگاری ارائه و توسط دستگاه نظارت مورد تایید قرار میگیرد، انجام شود.
روش پرتونگاری باید حداقل در بر گیرنده نوع چشمه پرتونگاری و قدرت آن، نوع دستگاه پرتونگاری و میزان نشت مجاز آن، نوع فیلم و نحوه ظهور و ثبوت آن، شاخصهای کیفیت فیلم، استاندارد قبولی فیلمها، علامتگذاری فیلمها، صلاحیت پرتونگارها و ملاحظات ایمنی باشد. پرتونگاری از جوشها باید بر طبق روش پرتونگاری تایید شده و با رعایت ملاحظات ایمنی مربوطه انجام شود و مسئولیت رعایت ملاحظات ایمنی بر عهده شرکت پرتونگار میباشد.
در صورتی که در پرتونگاری از جوشهای هر جوشکار در دو روز متوالی بیش از 6 درصد تعمیری و یا جوش بریدنی وجود داشته باشد، دستگاه نظارت میتواند از ادامه کار جوشکار جلوگیری نماید.
د- تفسیر فیلمهای رادیوگرافی
معیار قبولی جوشهای لولههای فولادی گاز باید طبق استاندارد API-1104 و بند 17-5-6-5 بخش جوشکاری از قسمت اول این مبحث باشد.
تفسیر فیلمهای پرتونگاری لولههای گاز باید به وسیله مفسرینی که دارای مدرک معتبر بینالمللی صلاحیت ASNT Level II در زمینه پرتونگاری و تفسیر فیلم جوش باشند صورت گیرد.
17-14-2 جوشکاری شبکههای گازرسانی پلی اتیلن
17-14-2-1 تعیین صلاحیت جوشکار
الف-کلیه جوشکاران باید در دورههای آموزشی مورد تأیید مراجع ذیصلاح، شرکت نموده و دورههای مربوطه را با موفقیت گذرانیده و گواهینامه دریافت نمایند.
ب- کلیه جوشکاران باید درآزمایش جوشکاری بر اساس استاندارد API 1104 شرکت نموده و مورد تأیید دستگاه نظارت قرار گیرند.
تذکر: حداقل مدرک تحصیلی جوشکاران باید دیپلم متوسطه (یا سیکل با 5 سال سابقه در جوشکاری) باشد.
17-14-2-2 آمادهسازی لولههای پلی اتیلن قبل از عملیات جوشکاری
الف- بازرسی لولهها
هر شاخه یا حلقه لوله قبل از آمادهسازی باید بازرسی گردد. لولههایی که دارای هر نوع عیب از قبیل کج بودن و دو پهن بودن دهانه، برآمدگی، شیار و فرورفتگی، خراش و حفره باشد باید کنار گذارده شوند تا توسط دستگاه نظارت و در صورت لزوم بازرس فنی ذیصلاح بررسی و دستور وازده شدن، تعمیر و یا برش آنها جهت از بین بردن نقص داده شود. قبل از جوشکاری لولهها به یکدیگر باید اطمینان حاصل نمود که داخل لولهها عاری از هر گونه خاک و اشیاء خارجی میباشد.
ب- تمیزکردن لبه لولهها
قبل از اتصال لولهها باید سطوح داخلی و خارجی آنها با پارچه مناسب از خاک وسایر مواد خارجی تمیز شود.
پ- برش لولهها
برش لولهها باید توسط وسایل مخصوص برش که مورد تأیید دستگاه نظارت میباشد انجام گیرد. مقطع بریده شده باید عمود برمحور طولی لوله باشد. برش فارسی بر[1] جهت لوله و اتصالات مجاز نمیباشد.
ت- جهت و انحراف لوله
1- کمانی شدن لوله: کمانی شدن لوله برای تغییرجهت مجاز بوده و حداقل شعاع کمان لوله باید 25 برابر قطر خارجی آن باشد. قرار گرفتن جوش در مسیر کمانی شدن لوله مجاز نبوده و باید کمانی شدن به صورتی انجام شود که لوله دچار چین و چروک نگردیده و دو پهن نشود. هرگاه چنین نواقصی ایجاد گردد لوله وازده خواهد شد و در صورتی که خم با شعاعهای خیلی کوچک مورد نظر باشد باید از اتصال و یا خمهای پیشساخته در کارخانه استفاده نمود.
ث-لولههای وازده
لولههای وازده شده باید با علامت (وازده) که بر روی آنها با رنگ متمایز (نقرهای یا سربی) نوشته میشود مشخص گردند. این گونه لولهها باید بلافاصله از محل کار خارج شده و در انبار مخصوص وازده نگهداری شود.
17-14-2-3 مشخصات فنی عملیات جوشکاری لوله و اتصالات پلی اتیلن
مطالب زیر شامل حداقل مشخصات فنی حاکم بر انواع جوشکاری لوله و اتصالات پلی اتیلن و دستگاهها وسایل مورد استفاده میباشد.
دستگاه نظارت مجاز خواهد بود که در تمام اوقات از کارگاه بازدید نموده و به کلیه اطلاعات مربوط به جوشکاری، آزمایشات جوش و غیره دسترسی داشته باشند.
– انواع جوشکاری توسط دستگاههای مختلف و با استفاده از روش الکتروفیوژن انجام خواهد شد.
– دستگاههای جوشکاری، گیرههای همترازی سر لولهها، دستگاهها و ابزار برش و تراش و دیگر تجهیزات و نیز محلول تمیز کننده باید از نوع مورد تأیید دستگاه نظارت بوده و در وضعیت خوب نگهداری شوند.
– در مورد نصب سه راهی انشعاب باید از زین مخصوص جوشکاری نوع الکتروفیوژن استفاده نمود.
– مناسب بودن اوضاع جوی برای انجام جوشکاری توسط دستگاه نظارت مشخص خواهد شد. درهر حال جوشکاری در دمای محیط کمتر از سه درجه سانتیگراد و همچنین در هوای برفی و بارانی بدون استفاده از چتر مخصوص مجاز نخواهد بود.
– در زمان جوشکاری و پس از آن تا سرد شدن کامل جوش، محل جوش و لولهها و اتصالات به هم جوش شده باید در گیره باقی مانده و نباید تحت هیچگونه تنشی قرار گیرد.
– در خاتمه هر روز کاری یا هر قسمت از کار و همچنین در تقاطعهای مختلف، دهانههای ابتدا و انتهایی کلیه لولههای جوشکاری شده باید توسط درپوش مناسبی بسته شوند تا از ورود خاک و زباله و حیوانات کوچک و آب و دیگر اجسام خارجی جلوگیری گردد. این در پوشها تا زمان شروع مجدد کار نباید برداشته شوند.
– جوشکاری اتصال نهایی[2] و اتصالات در داخل کانال باید به دقت کامل مطابق روشی که مجری برای این مورد پیشنهاد نموده و به تأیید دستگاه نظارت رسیده باشد، انجام گردد. در این حالات لولهها باید به دقت همتراز شوند بهطوری که تنشهای بجا مانده یا تنشهای واکنشی حاصل از جوشکاری به حداقل برسد. برای جفت کردن لولهها هنگام جوشکاری اتصال نهائی ممکن است تغییر در شیب کانال الزامی باشد. انشعابگیری گرم[3] و تزریق گاز حداقل یک ساعت پس از پایان جوشکاری باید انجامپذیرد.
– فاصله دو جوش متوالی در روی خطوط لوله پلیاتیلن محدودیت ندارد و باید انجام عملیات جوشکاری با قرار گرفتن لوله در درون گیره همترازی انجام شود.
– جوشکاری لولهها در محل خم مجاز نمیباشد.
– هر جوشکار باید شمارهای را به عنوان کد شناسایی که توسط دستگاه نظارت در زمان ارزیابی و آزمایش برای او تعیین شده با قلم مخصوص مجاور قسمتی از جوش که به وسیله خود او انجام شده در ربع بالای لوله یادداشت کند. برای علامتگذاری جوشها باید قلم مخصوص توسط مجری در اختیارجوشکاران قرار داده شود. اگر جوشکار به هردلیل کار را ترک کند کد شناسایی وی نباید توسط جوشکار دیگری مورد استفاده قرار گیرد.
چنانچه جوشکار به هر دلیل بیشتر از مدت سه ماه جوشکاری ننموده و مایل به بازگشت به سر کار خود باشد، لازم است مجدداً در آزمایش شرکت نماید و در صورت قبولی کد شناسایی جدیدی به وی داده شود.
الف- روشهای متداول جوشکاری لوله و اتصالات پلی اتیلن
روشهای مختلفی در جوشکاری لولهها و اتصالات پلی اتیلن جهت شبکهگذاری وجود دارند ولی در این مقررات فقط استفاده از روش جوشکاری الکتروفیوژن مجاز میباشد.
در این نوع جوشکاری از اتصالات نوع الکتریکی استفاده میشود، نظر به اینکه در این روش وسایل جوشکاری نقش مهمی در امر کیفیت جوش ایفا مینماید. لذا دستگاه جوشکاری باید مطابق استاندارد شرکتملّی گاز ایران و مورد تایید دستگاه نظارت باشد.
برای دستیابی به یک اتصال (جوش) خوب باید:
الف- سطوح جوشکاریکاملاً تمیز باشند.
ب- وسایل و ابزار مورد استفاده برای عملیات جوشکاری باید آزمایش شده و آماده کار باشد.
17-14-2-4 روش و مراحل انجام جوشکاری شبکه و انشعابات پلی اتیلن به روش الکتروفیوژن
روش و مراحل جوشکاری شبکه و انشعابات پلی اتیلن به روش الکتروفیوژن باید به ترتیب ذیل باشد:
1. ماشین جوش، تجهیزات، ابزار، لوله و اتصالات از نظر تطابق با مشخصات فنی و آماده به کار بودن باید کنترل شوند.
2. عمود بودن سر لوله کنترل شده و در صورت لزوم اصلاح شود.
3. لایه اکسید از سطوح جوشکاری لوله و اتصالات فاقد سیم به وسیله تراشنده استاندارد باید به طور کامل حذف شوند. حداکثر میزان تراش سطح لوله از 0/2 میلیمتر نباید تجاوز نماید.
تبصره: تراشیدن ناقص و یا بکار بردن هر گونه تراشنده غیراستاندارد از قبیل تیغ موکت بری، شیشه، سمباده کاغذی، برس برقی، سوهان، کاردک و هر وسیله خراش دهنده ممنوع است.
4. باید سطوح جوشکاری (سطح خارجی لوله و سطح داخلی اتصال و سطح خارجی اتصال فاقد سیم) به وسیله پارچه نخی سفید رنگ بدون پرز و آغشته به مایع تمیز کننده مجاز از هر گونه چربی و آلودگی پاک شوند.
محلولهای تمیز کننده مجاز عبارتند از: الکل اتیلیک سفید، استن، ایزوپروپانل با خلوص بالای 97 درصد.
5. میزان فرورفتن اجزاء جوش (لوله و اتصالات) با ماژیک مناسب علامتگذاری شود.
6. اجزاء جوش در یکدیگر و در گیره قرار داده شود.
7.باید عدم جابجایی اجزاء جوش کنترل شود. علائم میزان فرورفتگی بند (ث) فوق نباید جابجا شده باشد.
8- جوشکاری بر اساس دستورالعمل سازنده دستگاه و اتصال الکتروفیوژن انجام شود.
9- بالا زدن نشانگر جوش مشاهده شود.
10- رعایت زمان سرد شدن اول بر اساس زمان درج شده روی اتصال که در این مدت به هیچ وجه نباید گیرهها باز شود.
11- رعایت زمان سرد شدن دوم به میزان بیست دقیقه پس از زمان بند 10 خواهد بود که پس از انقضای این مدت میتوان لوله را جابجا و دفن نمود.
12- رعایت زمان سرد شدن سوم به میزان دو ساعت در صورتی که قرار باشد محل جوش تحت آزمون مقاومت و نشتی با فشار 100 پوند بر اینچ مربع قرار گیرد. زمان سرد شدن مذکور در شرایط تعمیرات و اتصال نهایی میتواند به مدت یک ساعت تقلیل یابد.
17-14-2-5 بازرسی و کنترل کیفیت جوشکاری شبکههای گازرسانی پلی اتیلن
به منظور حصول اطمینان از کیفیت مطلوب عملیات اجرایی شبکههای گازرسانی با لولههای پلی اتیلنی و جوشکاری به طریق الکتروفیوژن، بازرسی و آزمایشهای مختلفی طبق این بخش باید به عمل آید.
الف- احراز صلاحیت جوشکاران، بازرسی دستگاهها و متعلقات جوشکاری به طریق الکتروفیوژن باید انجام شود.
الف-1- کلیه جوشکاران باید علاوه بر آموزش دارای گواهینامه معتبر بوده و اعتبار گواهینامههای آنها مورد بررسی و تأئید دستگاه نظارت قرار گیرد.
الف-2- دستگاههای جوشکاری باید مطابق مشخصات فنی IGS-PL-016 بوده و سلامت وکارآئی کالیبره بودن آن مورد بررسی و تائید دستگاه نظارت قرار گیرد.
ب- استفاده از گیرههای همترازی مناسب جهت ثابت نگهداشتن اجزاء جوش الزامی است.
ب-1 سایر متعلقات و ابزار مورد استفاده برای جوشکاری از جمله محلولهای تمیز کننده از نقطه نظر مجاز بودن، کارآیی و خلوص باید در شروع پروژه مورد بررسی و تائید دستگاه نظارت قرار گرفته و در ادامه پروژه توسط دستگاه نظارت کنترل گردد.
پ- بازرسی ظاهری لوله و اتصالات قبل از جوشکاری: لوله و اتصالات قبل از مصرف باید از نقطه نظرهای زیر توسط مجری به طور دقیق مورد بازدید و بررسی قرار گیرد:
پ-1- سطوح ظاهری لوله و اتصالات سالم بوده و عاری از هرگونه ترک، شیار و برآمدگی یا فرورفتگیهای غیرقابل قبول باشد. حداکثر عمق شیار یا خراش سطحی تحت هیچ شرایطی نباید بیشتر از 10 درصد ضخامت لوله باشد.
پ-2- لوله و اتصالات باید گرد و مدور بوده و فاقد دو پهنیهای غیرقابل قبول باشد. ابعاد لولههای مصرفی از نظر رواداری (تلرانس) قطر خارجی و میزان مجاز دو پهنی باید به شرح جدول شماره پ-4-11 بخش پیوست باشد.
پ-3- حداکثر اختلاف قطر (دوپهنی) داخلی اتصال (در ناحیه ذوب) نباید از 1/5 درصد قطر اسمی تجاوز نماید.
پ-4- در صورت مشاهده لوله و اتصالات معیوب، این اقلام باید جداسازی و جهت بررسی و تصمیمگیری نهائی به دستگاه نظارت ارائه شود.
ت- بازرسی حین جوشکاری برای جوش الکترو فیوژن فرآیند جوشکاری مشتمل بر عملیات زیر باید به صورت کامل و با دقت توسط مجری کنترل گردد.
ت-1- اطمینان از سلامت دستگاه جوشکاری و وسائل و ابزار مورد استفاده
ت-2- مدور و عمود بودن سر لوله
ت-3- تمیزکاری سطوح جوشکاری
ت-4- تراشیدن کامل لایه اکسید از سطح جوشکاری لوله یا محل انشعاب اتصال فاقد سیم[4] با ابزار مناسب و تائید شده
ت-5- اطمینان از مناسب بودن پارچه (تمیز، سفید و فاقد پرز) و حلال مصرفی و پاک کردن هرگونه چربی و آلودگی از سطوح جوشکاری و جلوگیری از آلودگی مجدد سطوح جوشکاری در هنگام عملیات
ت-6- علامتگذاری میزان داخل رفتگی لوله در اتصال مورد جوشکاری با ماژیک مناسب
ت-7- قراردادن اجزاء جوش در یکدیگر و تثبیت آنها در گیره
ت-8- اطمینان ازعدم جابجائی اجزاء جوش پس از علامتگذاری
ت-9- اعمال پارامترهای جوشکاری براساس دستورالعمل سازنده اتصال پلی اتیلن
ت-10- حصول اطمینان از اتمام جوشکاری و اعمال زمان سرد شدن و رعایت زمان بازکردن گیرهها و عدم جابجائی اجزاء جوش
ث- ثبت مشخصات جوش:
کلیه اطلاعات مربوط به هر سرجوش شامل شماره جوش، محل جوش، مشخصات جوشکار، تاریخ و ساعت همراه با نتایج کنترلهای ده گانه بند (ت) فوق باید در یک برگه چک لیست که شناسنامه جوش میباشد به منظور ردیابی و سهولت مراجعات بعدی توسط مجری و با تائید دستگاه نظارت ثبت گردد.
ج- کنترلهای لازم پس از جوشکاری
با پایان یافتن فرآیند جوشکاری موارد زیر باید توسط مجری به طور کامل مورد بازدید عینی قرار گیرد:
ج-1- مشاهده بالا زدن نشانگر جوش
ج-2- مواد مذاب به هیچ وجه نباید در طول جوشکاری از طرفین و اطراف اتصال بیرونزده باشد.
ج-3- آثار تراشیدن و برداشتن لایه اکسید باید به طور پیوسته و کامل تمام سطوح و محدوده محل جوش را شامل گردد. تراشیدن به صورت ناقص قابل قبول نخواهدبود.
ج-4- پس از جوشکاری نباید هیچگونه تغییرشکل در موضع جوشکاری اتفاق افتاده باشد.
ج-5- علاوه بر کنترل دائمی عملیات اجرایی جوشکاری مجری، دستگاه نظارت باید از حسن انجام موارد فوق اطمینان حاصل نموده و به منظور بررسی کیفیت جوشهای پروژه نسبت به نمونهگیری لازم جهت انجام آزمایشهای لهیدگی به شرح مندرج در بند 17-14-2-6 اقدام نماید.
17-14-2-6 آزمایشهای مخرب
الف- نمونهگیری و انجام آزمایشهای لهیدگی و ارزیابی آن برای جوشهای نوع الکتروفیوژن برای حصول اطمینان از کیفیت جوشهای شبکه پلی اتیلن، آزمایش لهیدگی به صورت میدانی (در سایت اجرای پروژه) به شرح زیر باید انجام شود:
ب- روش نمونهگیری
ب-1- 25 سرجوش اول:
در آغاز عملیات جوشکاری، باید از اولین 25 سرجوش انجام شده توسط هر جوشکار، دو نمونه به صورت اتفاقی به تشخیص دستگاه نظارت بریده شده و تحت نظارت ایشان آزمایش لهیدگی در محل اجرای پروژه انجام گردد (تعداد اتصالات کمتر از 25 عدد برای یک سازنده 25 عدد تلقی خواهد شد). نتیجه آزمایش یکی از حالتهای زیر را در بر خواهد داشت:
در صورتی که نتیجه آزمایش قابل قبول باشد، 25 سرجوش انجام شده مورد تائید است.
درصورتی که نتیجه آزمایش قابل قبول نباشد، تعداد نمونهها دو برابر شده و آزمایش تکرار میگردد. در صورتیکه نتیجه آزمایش مجدد نیز نشان دهنده وجود اشکال در یکی از جوشهای بریده شده باشد، کلیه جوشهای آن گروه مردود بوده و باید بریده مجدداً و با استفاده از اتصالات سایر سازندگان، یا با تعویض جوشکار و یا تعویض دستگاه جوش به تشخیص دستگاه نظارت نسبت به ادامه جوشکاری اقدام شود.
ب-2- ادامه آزمایشهای:
پس از تائید اولین گروه 25 تائی، در ادامه برای بقیه جوشهای پروژه، آزمایش به شیوه بند (الف) ولیکن در گروههای 50 تایی تکرار میشود.
پ- آزمایش لهیدگی
منظور از آزمایش لهیدگی تعیین کیفیت جوش الکتروفیوژن از جهت چسبندگی و امتزاج کامل آن است. این آزمایش برای قطرهای 25 تا 225 میلیمتر و برای اتصالات الکتروفیوژن قابل استفاده بوده که در محل و در دمای 18 الی 30 درجه سانتیگراد برای ارزیابی میدانی قابل انجام میباشد. پیمانکار برای انجام آزمایش لهیدگی میتواند از خدمات شرکتهای ذیصلاح استفاده نماید.
ت- آمادهسازی نمونهها
انواع اتصالات سوکتی الکتروفیوژن[5] باید بر اساس مشخصات جدول شماره پ-4-12 آمادهسازی شوند.
ث- ارزیابی جوش
ث-1- در صورتی که هیچگونه جدایشی در اثر حرکات آرام پیچ گوشتی (طبق بند فوق) مشاهده نشد، جوش قابل قبول است.
ث-2- چنانچه حداکثر تا 2 حلقه سیمهای حرارتی از هر طرف و هر آزمایش جدا شود، کیفیت جوش قابل قبول است.
ث-3- در صورتی که بیش از 2 حلقه یا به طور کامل قطاع اتصال از لوله جدا شود کیفیت جوش قابل قبول نیست.
17-14-2-7 آزمایش غیرمخرب جوش سه راهی انشعاب زینی
جهت حصول اطمینان از صحت و استحکام جوش سه راهی انشعاب زینی پلی اتیلن به لوله اصلی لازم است پس از جوشکاری سه راهی انشعاب و پس از سرد شدن، قبل از سوراخ نمودن لوله اصلی، آزمایش فشار طبق دستورالعمل IGS-C-DN-04(0) انجام گیرد.
[1] – MITER
[2] – HOT TIE- IN
[3] – Hot Tap
[4] – Spigot
[5] – Electro Fusion Socket Type Fitting