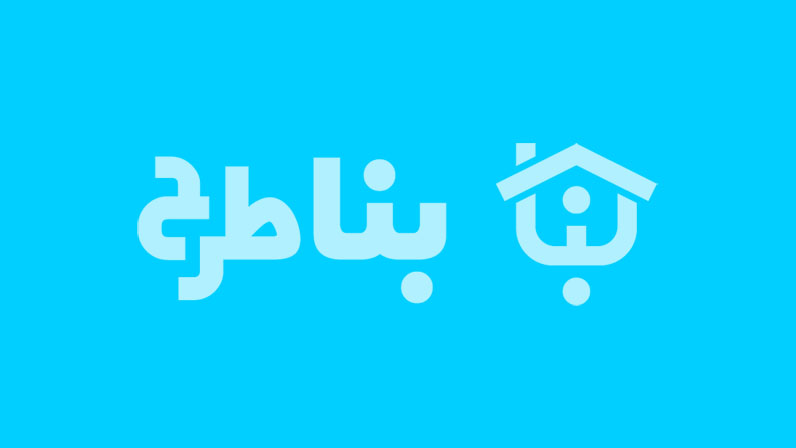
17-13 عایقکاری لولهها (بخش دوم لولهکشی گاز طبیعی با فشار 2 الی 60 پوند بر اینچ مربع)
17-13-1 کلیات
عایقکاری لولههای مدفون و توکار فولادی به دو روش زیر امکانپذیر است:
عایقکاری سرد (نوار پیچی) که عبارتست از عایقکاری لولهها با استفاده از نوارهای چسبدار و پرایمر مخصوص لوله.
عایقکاری گرم (عایقکاری با قیر) که عبارتست از عایقکاری لولهها با استفاده از قیر مذاب و الیاف پشم شیشه و پرایمر مربوطه.
تبصره: استفاده از سایر پوششها اعم از سرد یا گرم از جمله سایر انواع نوار، پوششهای اپوکسی دوجزئی، پوششهای پلی یورتان دوجزئی صد در صد جامد (پوششهای سرد) و قیر اصلاح شده، پلی اتیلن سه لایه و اپوکسی پودر (پوششهای گرم) در صورت مطابقت با استانداردهای شرکتملّی گاز و مقررات این مبحث بلامانع خواهد بود.
17-13-2 اقدامات اولیه قبل از عایقکاری
قبل از اقدام به عایقکاری لولهها باید اقدامات اولیه زیر در مورد آنها به عمل آید.
17-13-2-1 بازرسی ظاهری لولهها از نظر آلودگی به چربیها
هر نوع آلودگی لولهها به مواد چرب از قبیل گریس، مواد هیدروکربنی و چربیها باید با استفاده از حلالهای مناسب از جمله بنزین بدون سرب و یا تولوئن کاملا تمیز گردد و سپس با آب بدون املاح (در حد آب آشامیدنی) شسته شود.
17-13-2-2 بازرسی لولهها از نظر وجود عیوب مکانیکی
کلیه لولهها قبل از زنگ زدایی و تمیزکاری باید مورد بازرسی قرار گیرند و در صورت مشاهده هرگونه عیب مکانیکی از قبیل شیار، فرورفتگی، خراش، دو پهنی، صدمات وارده به سر لوله و حفرههای خوردگی کنار گذاره شوند تا به وسیله دستگاه نظارت بر طبق استانداردهای API-5L و IGS-M-PL-001(2) مورد ارزیابی قرار گرفته و تعیین تکلیف شوند.
17-13-2-3 بازرسی لولهها از نظر خشک بودن
لولهها قبل از زنگزدائی و تمیزکاری باید کاملا خشک باشند. در صورت وجود شبنم صبحگاهی بر روی سطح لوله و یا در صورتیکه دمای محیط کمتر از 5+ درجه سانتیگراد باشد، باید لولهها را با استفاده از مشعل گاز تا دمای 30+ درجه سانتیگراد پیش گرم نمود.
17-13-3 زنگ زدائی و تمیزکاری لوله ها
پس از بازرسی از لولهها، باید به وسیله مواد ساینده از قبیل شن و یا ذرات فولادی شات و گریت و به روش سندبلاست یا شات بلاست، لولهها را زنگزدائی و تمیزکاری و لایه زنگ یا اکسید تشکیل شده بر روی سطح لوله را کاملا بر طرف نمود.
در زنگزدائی و تمیزکاری لولهها به منظور جلوگیری از عوارض استفاده از شن در روش سندبلاست استفاده از ذرات سرباره مس یا "مسباره" ارجحیت دارد.
میزان تمیزی سطح لولهها باید بر طبق استاندارد ISO 8501-1 و درجه تمیزی آن برابر با درجه SA 2.5 باشد.
میزان زبری سطح لولهها باید بر طبق استاندارد ISO 8503-2 و مقدار زبری آن بین 50 الی 100 میکرون باشد.
لولههای زنگ زدائی و تمیز شده باید تا پایان روز کاری پرایمر زنی و یا عایقکاری شوند، در غیراینصورت لولهها بایدمجدداً زنگ زدائی و تمیزکاری شوند. در مناطق ساحلی و یا نقاطی که رطوبت نسبی بالای 80% باشد، لولههای زنگزدایی و تمیزکاری شده باید حداکثر پس از دو ساعت پرایمر زنی و یا عایقکاری شوند.
17-13-4 عایقکاری سرد لولهها (نوارپیچی)
عایقکاری سرد باید با استفاده از نوارهای چسبدار مخصوص عایقکاری لوله انجام شود، به این ترتیب که پس از پرایمر زنی، باید لولهها را در دو لایه شامل نوار زیر و نوار رو نوار پیچی نمود. در نوارپیچی سرد لولهها باید از نوار مخصوص سرجوش به عنوان نوار زیر، پرایمر مخصوص نوار سرجوش به عنوان پرایمر به علاوه نوار رو استفاده شود.
تبصره: استفاده از عایقهای سرد دیگر از جمله سایر انواع نوار، اپوکسیهای دو جزئی و پلی یورتانهای دو جزئی صد در صد خالص در صورت مطابقت با استانداردهای شرکتملّی گاز و مقررات این مبحث با نظر دستگاه نظارت بلامانع است.
در تهیه نوار و پرایمر باید دقت شود که نوار و پرایمر ساخت یک سازنده و قابل انطباق باشند.
استفاده از نوار و پرایمرکه ساخت سازندگان متفاوت باشند مجاز نمیباشد.
عایقکاری سرد باید در کارگاه و در محل سرپوشیده انجام شود. در صورتیکه به هر علت عایقکاری سرد در کارگاههای سرپوشیده امکانپذیر نباشد، باید از انجام عایقکاری در هوای بارانی، مه سنگین، گرد و غبار و در دمای زیر 5 درجه سانتیگراد خودداری شود.
17-13-4-1 پرایمر زنی
پرایمر زنی باید حتیالامکان بلافاصله پس از زنگ زدائی و تمیزکاری لولهها انجام شود. در صورت لزوم باید گرد و غبار سطح لوله به وسیله هوای فشرده زدوده شود.
پرایمر تا قبل از مصرف باید در بستهبندی اولیه نگهداری شود. قبل از باز کردن درب قوطی پرایمر برای مصرف، باید ظرف را به قدر کافی تکان داد و در صورت بزرگ بودن ظرف باید آن را بقدر کافی غلتاند تا مواد تهنشین شده پرایمر کاملا مخلوط شود. پس از استفاده از پرایمر باید بلافاصله درب ظرف را محکم نمود تا مواد فرار آن تبخیر نشود.
پرایمر زنی لولهها در هوای بارانی، مه سنگین، گرد و غبار و طوفان و در دمای زیر 5+ درجه سانتیگراد مجاز نمیباشد. در صورت وجود شبنم صبحگاهی باید سطح لوله کاملاًرا خشک نمود.
پرایمر زنی باید به وسیله قلم مو، غلطک و یا دستگاه اسپری انجام شود. پرایمر زنی باید به صورتی انجام شود که پس از خشک شدن ضخامت آن یکسان باشد و نقاط کمرنگ و یا پرایمر نخورده باقی نمانده باشد.
قبل از شروع نوار پیچی، پرایمر باید خشک شده باشد به نحوی که اثر انگشت روی آن باقی نماند. در مورد زمان خشک شدن پرایمر باید توصیه سازنده آن مورد توجه قرار گیرد.
17-13-4-2 نوار پیچی لایه اول
لایه اول نوار یا نوار زیرین، محافظت اصلی لوله درمقابل خوردگی را بر عهده دارد. نوار پیچی لایه زیرین باید به وسیله نوار سرجوش که مخصوص عایقکاری سرجوشها و اتصالات است و ضخامت لایه پلاستیک آن حداقل 0/2 میلیمتر و ضخامت لایه چسب آن حداقل 0/6 میلیمتر است انجام شود. نوارها باید تا قبل از مصرف در بستهبندیهای اولیه و در دمای مناسب و دور از تابش آفتاب و باران بر طبق توصیههای سازنده آنها نگهداری شوند. در استفاده از نوار و پرایمر باید توجه شود که هر دو ساخت یک سازنده و دارای تاریخ مصرف معتبر باشند. در صورتی که نوار پیچی بلافاصله پس از پرایمر زنی انجام نشود، میتوان لولههای پرایمر خورده را برای مدت حداکثر چهار هفته در مکان مناسب نگهداری نمود به نحوی که خواص پرایمر از بین نرود. در صورت از بین رفتن خواص پرایمر و یا پدیدار شدن آثار زنگزدگی، لولهها بایدمجدداً زنگ زدائی و تمیزکاری و سپس پرایمر زنی شوند. چنانچه بیش از یک روز از پرایمر زنی لولهها گذشته باشد، قبل از اقدام به نوار پیچی باید سطح پرایمر خورده را با برس زبر کرده و سپس اقدام به پرایمر زنی مجدد نمود.
نوار پیچی در هوای بارانی، مه سنگین، گرد و غبار و در دمای زیر 5+ درجه سانتیگراد مجاز نمیباشد.
نوار پیچی باید با زاویه ثابت و با کشش یکنواخت انجام شود. میزان کشش نوار باید در حدی باشد که بیش از 5 درصد از عرض نوار کم نشود. میزان روی هم پیچی نوار برای لایه اول باید برابر با پنجاه درصد عرض نوار باشد، به طوری که هر دور نوار، نصف عرض دور قبلی را بپوشاند.
با اتمام هر حلقه نوار باید نوار حلقه جدید حداقل 15 سانتیمتر روی انتهای نوار قبلی پیچیده شود.
برای اطمینان از چسبیدن نوار باید آن را با دست روی نوار قبلی فشرد.
در عبور لوله از نقاطی که سطح آبهای زیر زمینی بالا است و یا در تقاطع با نهرآب، باید نوار پیچی نوار زیرین در دو لایه با روی هم پیچی پنجاه درصد 50% انجام شود. در صورتیکه نوار پیچی لولهها در کارگاه انجام شود باید حدود 10 سانتیمتر از سرلولهها نوار پیچی نشود تا پس از انجام جوشکاری، همراه با قسمت سرجوش لولهها نوار پیچی شود.
17-13-4-3 نوار پیچی لایه دوم
نوار پیچی لایه دوم باید با استفاده از نوار رویی که ضخامت لایه پلاستیک آن 0/3 میلیمتر و ضخامت لایه چسب آن 0/2 میلیمتر است انجام شود.
نوار پیچی رویی برای محافظت از نوار زیرین انجام میشود. میزان روی هم پیچی نوار رویی باید حداقل 10% عرض نوار باشد.
در نوار پیچی نوار رویی باید حدود 15 سانتیمتر از سر لولهها نوارپیچی نشود.
17-13-4-4 نوار پیچی سرجوشها، اتصالات و نقاط تعمیری
در صورتی که لولهها در کارگاه نوارپیچی شده و سپس به محل اجرای لولهکشی حمل شوند، پس از انجام جوشکاری باید قسمت نوار پیچی نشده سر لوله و قسمت سرجوش در محل نوارپیچی شود. برای نوار پیچی سرجوش، ابتدا باید با استفاده از برس برقی یا برس دستی محل جوش و قسمتهای نوار پیچی نشده سر لوله را از پرایمر وسایر مواد خارجی پاک نمود به نحوی که سطح فلز لولهکاملاً براق شود. در صورت لزوم قطرات ناشی از جوش باید با استفاده از قلم برداشته شود. پرایمر زنی سرجوش باید با استفاده از پرایمر مخصوص نوار سرجوش انجام شود. پرایمر زنی سرجوش باید علاوه بر روی قسمتهای لخت لوله و محل جوش، بر روی حداقل 5 سانتیمتر از نوارپیچی نوار زیر لوله در دو طرف جوش انجام شود.
پس از خشک شدن پرایمر باید نوار پیچی سرجوش با استفاده از نوار سرجوش و با روی هم پیچی 50% بر روی قسمتهای پرایمر خورده شامل محل جوش، قسمتهای نوارپیچی نشده و حداقل 5 سانتیمتر بر روی نوار زیر لولههای طرفین سرجوش انجام شود. سپس باید نوار رو با روی هم پیچی حداقل 10% بر روی نوارپیچی نوار سرجوش انجام شود.
در صورت زخمی شدن نوار، باید قسمت معیوب نوارپیچی برداشته شود. سپس محل عیب به اضافه حدود 5 سانتیمتر از هر طرف روی نوار پیچی نوار زیر با استفاده از پرایمر مخصوص نوار سرجوش، پرایمر زنی شود و پس از خشک شدن پرایمر، با استفاده از نوار سرجوش نوارپیچی شود. سپس نوارپیچی نوار رویی نیز به روشی که برای سرجوشها ذکر گردید، انجام شود.
17-13-4-5 کنترل کیفیت عایقکاری سرد
پس از اتمام نوار پیچی نوار زیر، با استفاده از دستگاه منفذیاب (هالیدی دیتکتور) که مورد تائید دستگاه نظارت قرار گرفته باشد باید از سالم بودن نوار پیچی اطمینان حاصل نمود.
نوار پیچی انجام شده باید از نظر ظاهری یکنواخت بوده و فاقد چین و چروک باشد. برای اطمینان از کیفیت نوار و پرایمر استفاده شده و همچنین اطمینان از کیفیت نوارپیچی باید بر روی نوار زیر به طریق زیر آزمایش چسبندگی انجام داد. ابتدا با چاقو دو شیار موازی به فاصله یک سانتیمتر از یکدیگر بر روی نوار زیر در جهت عمود بر محور طولی لوله ایجاد کنیم. سپس با برش عرضی محل شروع دو شیار را بهم وصل نموده و با نوک چاقو قسمت ابتدای نوار بریده شده را از سطح لوله بلند کرده و با نیروی یکنواخت در جهت عمود بر سطح لوله نوار زیر را از لوله جدا میکنیم. انجام آزمایش چسبندگی باید حداقل دو ساعت بعد از نوارپیچی و در دمای بین 15 تا 25 درجه سانتیگراد باشد.
چسبندگی نوار باید در حدی باشد که، نوار با نیرویی بیش از 1/5 کیلوگرم نیرو به ازای هر سانتیمتر عرض نوار، از سطح لوله جدا شود و لایه چسب نوار به صورت یکنواخت هم بر روی نوار و هم بر روی لوله باقی بماند.
پس از اتمام نوارپیچی سرجوشها، شیرها، اتصالات و نقاط تعمیری و قبل از خوابانیدن لوله در کانال، باید کل طول لوله نوارپیچی شده مجدداً با استفاده از دستگاه منفذیاب (هالیدی دتکتور) بر طبق دستورالعمل مندرج در بخش 17-13-5-7 مورد آزمایش قرار گیرد تا از سالم بودن نوار پیچی انجام شده اطمینان حاصل شود.
17-13-5 عایقکاری گرم لولهها (عایقکاری با قیر)
17-13-5-1 کلیات
این بخش مربوط به عایقکاری گرم لولهها شامل استفاده از قیر پایه نفتی، پرایمر مخصوص موسوم به پرایمر مصنوعی و نوارهای پشم شیشه داخلی و قیراندود خارجی میباشد.
عایقکاری گرم لولهها با استفاده از قیر مذاب و نوارهای پشم شیشه داخلی و خارجی و پرایمر مربوطه انجام میشود. در تهیه مواد عایقکاری گرم باید قیر و پرایمر از یک سازنده تهیه شود. استفاده از قیر و پرایمر ساخت سازندگان متفاوت مجاز نیست.
تبصره: استفاده از سایر انواع عایقهای گرم از جمله، قیر ذعال سنگی، قیر اصلاح شده، پلی اتیلن سه لایه و اپوکسی پودر در صورت مطابقت با استانداردهای شرکتملّی گاز و مقررات این مبحث با نظر دستگاه نظارت بلامانع است.
17-13-5-2 شرایط محیط برای عایقکاری گرم
عایقکاری گرم باید در کارگاه و در محل سرپوشیده انجام شود. در صورتیکه به هر علت عایقکاری گرم در کارگاههای سرپوشیده امکانپذیر نباشد، باید از انجام عایقکاری گرم در هوای بارانی، مه سنگین، گرد و غبار و در دمای زیر بوسیله 5+ درجه سانتیگراد خودداری شود.
17-13-5-3 اقدامات اولیه قبل از عایقکاری گرم لولهها
اقدامات اولیه قبل از عایقکاری گرم لولهها باید بر طبق بند 17-13-2 انجام شود.
17-13-5-4 عملیات عایقکاری گرم لولهها
پس از اقدامات اولیه عایقکاری گرم، باید پرایمر زنی طبق بند 17-13-4-1 انجام شود.
عایقکاری با قیر باید با ماشینآلات مخصوصی که به صورت ثابت در کارگاههای سرپوشیده، قیر پاشی و نوار پیچی را به صورت توأم انجام میدهد، باشد. ماشینآلات عایقکاری گرم عبارتند از:
– دیگ ذوب قیر که باید مجهز به همزن مکانیکی، دماسنج و در دهانه خروجی مجهز به یک توری سیمی با ابعاد چشمه حداکثر 1/5 میلیمتر باشد.
– دستگاه نوار پیچی که برای نوارپیچی نوار پشم شیشه داخلی و نوار پشم شیشه قیراندود خارجی بکار میرود.
– دستگاه پرایمر زنی ثابت
انجام عایقکاری گرم باید طبق مشخصات زیر انجام شود:
– قیر را باید بر روی سکوهای بتنی خرد نمود تا از آلوده شدن آن به خاک و مواد خارجی جلوگیری شود.
– قیر باید طبق دستورالعمل سازنده آن ذوب گردد و انجام عایقکاری گرم در درجه حرارت تعیین شده به وسیله سازنده قیر صورت گیرد.
– نوارهای پشم شیشه داخلی و نوار پشم شیشه قیر اندود خارجی باید تا قبل از مصرف در بستهبندیهای اولیه و در دمای مناسب و دور از تابش آفتاب و باران بر طبق توصیههای سازنده آنها نگهداری شوند.
– در صورتی که عایقکاری گرم بلافاصله بعد از پرایمر زنی انجام نشود، میتوان لولههای پرایمر خورده را برای مدت حداکثر چهار هفته در مکان مناسب نگهداری نمود به نحوی که خواص پرایمر از بین نرود. در صورت از بین رفتن خواص پرایمر و یا پدیدار شدن آثار زنگزدگی، لوله بایدمجدداً زنگ زدائی و تمیزکاری و پرایمر زنی شود.
– در صورتی که بیش از یک روز از پرایمر زنی لولهها گذشته باشد، قبل از اقدام به عایقکاری گرم باید سطح پرایمر خورده لوله را با برس زبر کرده و سپس اقدام به پرایمر زنی مجدد نمود.
– نوار پیچی نوارهای پشم شیشه داخلی و نوار پشم شیشه قیر اندود خارجی باید با زاویه ثابت و با کشش یکنواخت و مناسب توسط دستگاه قابل تنظیم انجام شود.
– میزان روی هم پیچی نوارهای پشم شیشه داخلی و نوار پشم شیشه قیر اندود خارجی باید حداقل ده درصد از عرض نوار باشد.
– حداقل ضخامت عایقکاری گرم لولهها باید چهار میلیمتر باشد.
– در عایقکاری گرم لولهها باید حدود 10 سانتیمتر از سرلولهها عایقکاری نشود تا پس از انجام جوشکاری، همراه با سرجوش نوار پیچی شوند.
پس از اتمام عایقکاری به منظور جلوگیری از تاثیر اشعه ماوراء بنفش خورشید بر روی پوشش قیری لوله باید با استفاده از محلول شیر آهک که با ترکیب زیر تهیه شده باشد لولهها را سفید شوئی نمود:
– 30 کیلو گرم آهک
– 100 لیتر آب
– 2 کیلوگرم روغن برزک
– 2 کیلو گرم نمک طعام
پس از اتمام عایقکاری لولهها و قبل از خارج شدن لوله از خط تولید، باید با استفاده از دستگاه منفذیاب (هالیدی دیتکتور) بر طبق دستورالعمل مندرج در بند 17-13-5-7 از سالم بودن عایقکاری انجام شده اطمینان حاصل نمود.
17-13-5- 5 عایقکاری دوبله
در تقاطع لوله با کانال آب، نهرها، قنات، رودخانهها و یا نقاطی که سطح آبهای زیرزمینی بالا است و یا در تقاطع با راهآهن، جادهها و خیابانهای اصلی، عایقکاری لولهها باید به صورت دوبله انجام شود. در عایقکاری دوبله لولهها نوار پشم شیشه زیری باید در دو لایه پیچیده شود و حداقل ضخامت کل عایق لوله باید شش میلیمتر باشد.
17-13-5-6 عایقکاری سرجوشها، اتصالات و نقاط تعمیری
برای عایقکاری سرجوشها، اتصالات و شیر آلات و نقاطی که پوشش آنها آسیب دیده است، پس از انجام جوشکاری باید قسمت عایقکاری نشده سر لولهها و سرجوشها با استفاده از نوار سرجوش با چسب نوع پایه قیری در محل نوارپیچی شوند.
برای نوار پیچی سرجوشها ابتدا باید با استفاده از برس برقی یا برس دستی محل جوش و قسمتهای عایقکاری نشده سر لولهها را از مواد خارجی پاک نمود به نحوی که سطح فلز لولهکاملاً براق شود. در صورت لزوم باید قطرات ناشی از جوش با استفاده از قلم برداشته شود. قبل از عایقکاری سرجوش باید قسمت تمیز شده سر جوش و سطح لوله در طرفین جوش به اضافه حداقل 5 سانتیمتر از عایقکاری گرم لوله در هر طرف را به وسیله پرایمر مخصوص نوار سرجوش پایه قیری پرایمر زنی کرد.
پس از خشک شدن پرایمر باید نوار پیچی سرجوش با استفاده از نوار سرجوش و با روی هم پیچی 50% بر روی قسمتهای پرایمر خورده شامل محل جوش، قسمتهای عایقکاری نشده لولههای طرفین جوش و حداقل 5 سانتیمتر بر روی عایقکاری لولههای طرفین سرجوش، انجام گیرد. سپس لایه دوم نوار نیز به روشی که برای سرجوشها ذکر گردید انجام شود.
در صورت زخمی شدن عایقکاری لوله، باید قسمت معیوب عایق لوله در محل عیب به صورت دور تادور برداشته شده و محل تمیزکاری شود. محل باز شده به اضافه حدود 5 سانتیمتر از دو طرف عایق لوله پرایمر زنی شده و با استفاده از نوار سرجوش با چسب نوع پایه قیری نوارپیچی شود. سپس لایه دوم نوار نیز به روشی که برای سرجوشها ذکر شد، انجام شود.
پس از اتمام نوارپیچی سرجوشها، اتصالات و نقاط تعمیری و قبل از خوابانیدن لوله در کانال، باید با استفاده از دستگاه منفذیاب (هالیدی دتکتور) بر طبق دستورالعمل مندرج در بخش 17-13-5-7 از سالم بودن عایقکاری انجام شده اطمینان حاصل نمود.
پس از اتمام عایقکاری سرجوشها، شیرها، اتصالات و نقاط تعمیری و قبل از خوابانیدن لوله در کانال، باید کل طول لوله عایقکاری شده مجددأ با استفاده از دستگاه منفذیاب بر طبق دستورالعمل مندرج در بخش 17-13-5-7 مورد آزمایش قرار گیرد تا از سالم بودن نوار پیچی انجام شده اطمینان حاصل شود.
تبصره: در انجام عملیات تعمیر پوشش حداکثر سطح تعمیر شده نباید از ده درصد سطح لوله بیشتر شود. در صورت تجاوز از مقدار مذکور، پوشش آن لوله قابل قبول نیست و باید مجدداً پوشش گردد.
17-13-5-7 آزمایش و کنترل کیفیت عایقکاری گرم
آزمایش و کنترل کیفیت عایقکاری گرم باید بر اساس مقررات این بند به شرح زیر صورت گیرد.
1- بازرسی ظاهری – عایقکاری باید از نظر ظاهری یکنواخت بوده و فاقد چین و چروک باشد.
2- آزمایش منفذیابی- پس از اتمام عایقکاری گرم، باید با استفاده از دستگاه منفذیاب بر طبق دستورالعمل ذیل از سالم بودن عایقکاری لولههای پوشش شده به صورت صد در صد اطمینان حاصل نمود.
در صورتی که عایقکاری لولهها به روش نوارپیچی انجام شده باشد، کلیه قسمتهای لوله پس از نوارپیچی لایه زیرین و قبل از نوارپیچی لایه روئی باید به وسیله دستگاه منفذیاب که مورد تایید دستگاه نظارت قرار گرفته باشد مورد آزمایش منفذیابی قرار گیرد. سرعت دستگاه بر روی لوله نباید بیش از 3/0 متر بر ثانیه باشد. جهت جلوگیری از آسیب دیدن پوشش لوله باید مراقبت نمود تا الکترود دستگاه بر روی هیچ یک از قسمتهای لوله توقف ننماید. تمام مراحل آزمایش با دستگاه منفذیاب پوشش باید در حضور دستگاه نظارت انجام گردد. به منظور تعیین میزان ولتاژ واقعی مورد نیاز جهت آزمایش با دستگاه منفذیاب، لازم است بر روی قسمتی از لوله که به وسیله نوار زیر و با روی هم پیچی پنجاه درصد نوارپیچی شده است، با نوک سوزن سوراخی در آن ایجاد کرد به طوری که نوک سوزن پس از عبور از لایههای نوار به سطح لوله برسد. پس از ایجاد سوراخ و پس از حرکت دادن روی نقطه سوراخ شده باید به تدریج ولتاژ دستگاه را افزایش داد تا حدی که جرقه بین الکترود و لوله در نقطه سوراخ شده ایجاد گردد. برای اطمینان از تنظیم دستگاه این آزمایش باید هر چهار ساعت یکبار انجام شود.
روش انجام آزمایش منفذیابی و تنظیم دستگاه منفذیاب پوشش لولههای عایقکاری شده با قیر دقیقأ مشابه با موارد ذکر شده برای لولههای نوارپیچی شده میباشد.
3- آزمایش چسبندگی- برای اطمینان از کیفیت قیر و پرایمر استفاده شده و همچنین اطمینان از کیفیت عایقکاری، باید به طریق زیر آزمایش چسبندگی در دمای بین 15 الی 25 درجه سانتیگراد انجام گردد:
ابتدا باید با چاقو دو شیار موازی به فاصله حدود سه سانتیمتر از یکدیگر بر روی نوار عایق لوله و در جهت عمود بر محور طولی لوله ایجاد کرد. سپس با برش عرضی، محل شروع دو شیار را به هم وصل و نوک چاقو را زیر قسمت ابتدای محل بریده شده قرار داده و پوشش قیری را از سطح لوله بلند کرده و با نیروی یکنواخت در جهت عمود بر سطح لوله پوشش قیری را از لوله جدا کرد. چسبندگی پوشش در صورتی مطلوب خواهد بود که پوشش به آسانی از سطح لوله جدا نشود و قیر به سطح لوله چسبیده و به صورت نقطه به نقطه از سطح لوله کنده شود.