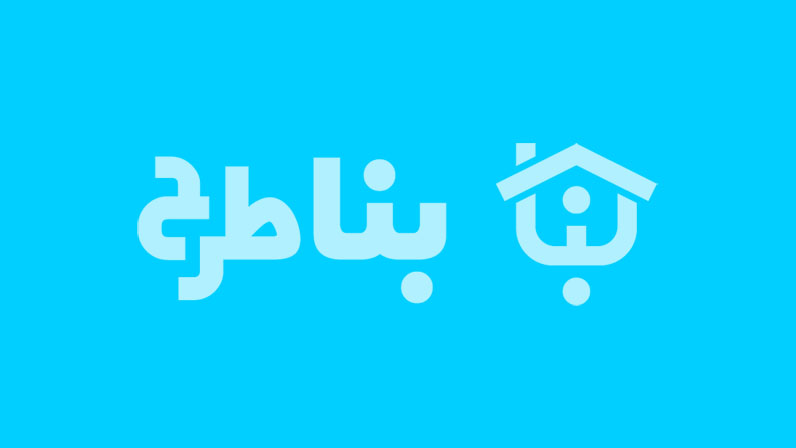
4-4-10 اتصال با جوش
4-4-10 اتصال با جوش
برای برقراری اتصالات جوشی رعایت مشخصات مندرج در آییننامه جوشکاری ساختمانی ایران[7] لازم است. علاوه بر مفاد آییننامه مورداشاره، رعایت الزامات بندهای زیر ضروری است.
1-4-4-10 کنترل کیفیت و تضمین کیفیت جوش
رئوس برنامههای مربوط به کنترل و بازرسی جوشکاری سازههای فولادی را میتوان در قالب پنج مورد زیر بیان نمود:
1- جوشکاران (Personnel)
2- فرایند جوشکاری (Process)
3- آمادهسازی درز جوش (Preparation)
4- دستورالعمل جوشکاری (Procedure)
5- بازرسی و تأیید (Prove)
فعالیتهای بازرسی جوش شامل کنترل کیفیت و تضمین کیفیت در سه مرحله قبل، حین و پس از جوشکاری انجام میشود که این سه مرحله در جداول 10-4-1 تا 10-4-3 ارائه شده است.
فعالیتهایی که باید توسط هر دو بخش کنترل کیفیت و تضمین کیفیت انجامپذیرد، میتواند به صورت همزمان با هماهنگی بین طرفین توسط یک شخص حقیقی یا حقوقی ثالث ذیصلاح انجامپذیرد. در این جداول فعالیتهای بازرسی مشمول یکی از دو حالت زیر است:
- مشاهده (O): بازرس مربوطه باید این موارد را مشاهده و بررسی نماید. این بررسی و مشاهده شامل تمامی موارد نشده و میتواند به صورت غیرمنظم انجام شود. به هر حال تعداد بازبینیها، رافع مسئولیت QC و QA نیست. در این حالت ادامه ساخت موکول به انجام
بازرسی نیست.
- انجام (P): این فعالیتها باید برای هر مورد انجامپذیرد و انجام مرحله بعدی منوط به صدور تأییدیه مرحله قبل میشود.
جدول 10-4-1: بازرسی قبل از جوشکاری
ردیف | شرح فعالیت | QC | QA |
1 | بررسی گواهینامه صلاحیت جوشکاران * | P | O |
2 | بررسی دستورالعملهای جوشکاری | P | P |
3 | بررسی گواهینامه مواد مصرفی جوش | P | P |
4 | قابل شناسایی بودن مواد و مصالح (نوع و رده) | O | O |
5 | سیستم شناسایی جوشکاران (علامتگذاری بند جوش) | O | O |
6 | کنترل تجهیزات جوشکاری | O | O |
7 | کنترل شکل و پرداخت سوراخ دسترسی | P | O |
8 | کنترل آمادهسازی درز جوش شیاری:
• آمادهسازی اتصال • هندسه (همراستایی، فاصله ریشه، عمق ریشه، پخ) • تمیزی درز جوش • وضعیت خال جوشکاری (کیفیت و محل خال جوش) • نوع پشتبند و مونتاژ آن |
P | O |
9 | کنترل آمادهسازی درز جوش گوشه:
• هندسه (فاصله ریشه، راستا، ….) • تمیزی درز جوش • وضعیت خال جوشکاری (کیفیت و محل خال جوش) |
O | O |
*برگزاری دورههای آموزشی جوشکاران و صدور گواهینامههای صلاحیت به آنها توسط مراکز ذیصلاح انجام گرفته باشد.
جدول 10-4-2: بازرسی حین جوشکاری
ردیف | شرح فعالیت | QC | QA |
1 | کنترل شرایط نگهداری و جابجایی الکترود:
• بستهبندی • زمان در معرض هوا بودن |
O | O |
2 | عدم جوشکاری روی ترکهای خال جوش | O | O |
3 | شرایط محیطی:
• سرعت باد • بارش و دما |
O | O |
4 | پیروی از WPS:
• تنظیم تجهیزات جوشکاری • سرعت جوشکاری • انتخاب الکترود و سیم جوش • نوع و دبی گاز محافظ • پیش گرمایش و دمای بین دو عبور • وضعیت جوشکاری (OH, V,H,F مطابق شکل 10-4-1) |
O | O |
5 | کنترل تکنیک جوشکاری:
• تمیزکاری بین دو عبور و عبور نهایی • هندسه جوش هر عبور • بازرسی کیفیت چشمی هر عبور |
||
6 | قرارگیری و نصب گل میخها | P | O |
*
شکل 10-4-1: چهار وضعیت اصلی جوشکاری برای جوشکاری با جوش گوشه
جدول 10-4-3: بازرسی پس از جوشکاری
ردیف | شرح فعالیت | QC | QA |
1 | کنترل تمیزکاری جوش | O | O |
2 | کنترل ابعاد جوش (بعد، طول و محل جوش) | P | P |
3 | بازرسی چشمی جوش:
• عدم وقوع ترک • امتزاج جوش با فلز پایه و عبورهای قبل • چاله جوش • هندسه مقطع جوش • بریدگی کناره جوش • تخلخل • لکه قوس |
P | P |
4 | بازرسیهای غیرمخرب | P | P |
5 | کنترل سوراخ دسترسی جوش مقاطع سنگین برای اطمینان از عدم تا ترکخوردگی | P | P |
6 | کنترل برداشتن پشتبند و ورق گوشواره (ناودان جوش) در صورت لزوم | P | P |
7 | کنترل جوش تعمیری | P | P |
8 | تهیه مستندات تأیید یا رد کیفیت قطعات جوشکاری شده | P | P |
9 | کنترل عدم جوشکاری در نواحی غیرمجاز | O | O |
10 | ناحیة k* | P | P |
* هنگام جوشکاری ورقهای مضاعف، ورقهای پیوستگی و سختکنندهها، بازرسی چشمی برای کشف ترک در ناحیه k ورق جان تا فاصله 75 میلیمتر بالا و پایین جوش انجام شود. ناحیة k مطابق شکل 10-4-2، به حدفاصل نقطه شروع گردی ریشه اتصال بال به جان تا 38 میلیمتر بعد از آن اطلاق میشود.
شکل 10-4-2: ناحیة k
2-4-4-10 آزمایشهای غیرمخرب جوش
آزمایش فراصوت (UT)، آزمایش ذرات مغناطیسی (MT)، آزمایش مواد نافذ (PT) و آزمایش پرتونگاری (RT) در صورت نیاز باید منطبق با ضوابط آییننامه جوشکاری ساختمانی ایران به وسیله واحد تضمین کیفیت انجام شود. در جدول 10-4-4 میزان آزمایشهای غیرمخرب جوش ارائه شده است. نتیجه تمام این آزمایشها باید در پروندههای مخصوص ثبت شده و با تفسیر در اختیار ناظر کارفرما قرار گیرند. تفسیر ناظر از نتایج آزمایش قطعی تلقی میگردد.
جدول 10-4-4: میزان آزمایشهای غیرمخرب جوش هنگام تولید و نصب
نوع جوش مورد آزمایش | نوع آزمایش | درصد آزمایشها برای گروهبندی اهمیت ساختمان مطابق استاندارد 2800 | ||
1 و 2 | 3 | 4 | ||
1- کلیه جوشها | بازرسی چشمی (VI) | 100 | 100 | 100 |
2- جوشهای لب به لب عرضی بالهای کششی، اعضای کششی خرپاها، یک ششم عمق جان تیرها در مجاورت بال کششی و جوش شیاری ورق روسری و زیرسری به ستون در اتصال صلب تیر به ستون | پرتونگاری با فراصوت (RT یا UT) | 100 | 20 | – |
3- جوشهای لب به لب طولی بالهای کششی و اعضای کششی خرپاها | پرتونگاری با فراصوت (RT یا UT) | 10 | 5 | – |
4- جوشهای لب به لب عرضی و طولی در بالهای فشاری و اعضای فشاری خرپاها و ستونها | پرتونگاری با فراصوت (RT یا UT) | 20 | 10 | – |
5- جوشهای لب به لب عرضی جان تیرها که شامل بند 2 فوق نیست و جوشهای لب به لب طولی جان تیرها | پرتونگاری با فراصوت (RT یا UT) | 20 | 10 | – |
6- جوش گوشه بال به جان و سختکنندهها | رنگ نافذ (PT) یا ذرات مغناطیسی (MT) | 10 | 10 | 5 |
7- جوشهای گوشه اتصالات مهاربندها و اتصالات تیر به ستون | رنگ نافذ (PT) یا ذرات مغناطیسی (MT) | 100 | 20 | 10 |
الزامات تکمیلی جدول 10-4-4 به شرح زیر است:
1) ورقهای با ضخامت کمتر یا مساوی 8 میلیمتر نیاز به آزمایش پرتونگاری (RT) یا فراصوت (UT) ندارند.
2) ساختمانهای گروه 3 دارای 7 طبقه یا بیشتر روی سطح زمین، مطابق گروههای 1 و 2 ارزیابی میشوند.
1-2-4-4-10 نرخ مردودی آزمایش پرتونگاری یا فراصوت[8]
نرخ مردودی آزمایش پرتونگاری یا فراصوت از تقسیم تعداد جوشهای معیوب به جوشهای کامل به دست میآید. جوشهایی که دارای ناپیوستگی در حد قابل قبول هستند، در هنگام تعیین نرخ مردودی نباید جزو جوشهای معیوب حساب شوند. برای ارزیابی نرخ مردودی جوشهای پیوسته با طول بیش از یک متر و گلوی مؤثر جوش حداکثر 25 میلیمتر، هر 300 میلیمتر به عنوان یک جوش در نظر گرفته میشود. برای ارزیابی نرخ مردودی جوشهای پیوسته با طول بیش از یک متر طول و گلوی مؤثر بیش از 25 میلیمتر، هر 150 میلیمتر به عنوان یک جوش در نظر گرفته میشود.
2-2-4-4-10 کاهش تعداد آزمایش پرتونگاری یا فراصوت
در پروژههایی که تعداد حداکثر 40 جوش داشته باشند، نباید هیچ کاهشی در میزان آزمایشهای پرتونگاری یا فراصوت صورت گیرد. در حالتی که در ابتدا مقرر شده باشد که 100 درصد جوشها تحت آزمایش پرتونگاری با فراصوت قرار گیرند، برای یک جوشکار مشخص میتوان این میزان را تا 25 درصد کاهش داد، مشروط بر آنکه نرخ مردودی جوشهای اجرا شده توسط آن جوشکار حداکثر 5 درصد باشد. در هر پروژه باید به تعداد حداقل 40 جوش کامل اجرا شده باشد تا این ارزیابی برای کاهش تعداد آزمایشها صورت گیرد.
3-2-4-4-10 افزایش تعداد آزمایش پرتونگاری یا فراصوت
در حالتی که از ابتدا مقرر شده باشد که 10 درصد از جوشها تحت آزمایش پرتونگاری یا فراصوت قرار گیرند، درصورتی که نرخ مردودی جوشهای اجرا شده توسط یک جوشکار مشخص بیش از 5 درصد باشد، این میزان باید به 100 درصد افزایش یابد. باید تعداد حداقل 20 جوش کامل قبل از اعمال این افزایشها اجرا شده باشد. اگر نرخ مردودی برای جوشهای اجرا شده توسط جوشکاری برای تعداد حداقل 40 جوش کامل به 5 درصد یا کمتر کاهش یابد، میزان آزمایشهای پرتونگاری یا فراصوت را مجدداً میتوان به 10 درصد کاهش داد.
4-2-4-4-10 مستندسازی
تمام آزمایشهای غیرمخرب اجراشده باید مستندسازی شوند. برای کارگاه ساخت، گزارش آزمایش غیرمخرب (NDT) باید جوش آزمایش شده را با اسم قطعه و موقعیت جوش معرفی کند. برای محل نصب گزارش آزمایش باید جوش آزمایش شده را بر حسب موقعیت آن در سازه، اسم قطعه و موقعیت جوش معرفی کند. اگر جوشی براساس آزمایش غیرمخرب مردود شده باشد، گزارش آزمایش غیرمخرب باید موقعیت عیب و علت مردودی را بیان کند.
3-4-4-10 ضوابط اجرایی
1-3-4-4-10 شرایط غیرمجاز جوشکاری
جوشکاری در شرایط زیر مجاز نیست:
الف) زمانی که دمای محیط کار کمتر از 10- درجه سلسیوس است.
ب) زمانی که دمای فلز پایه کمتر از مقادیر ذکر شده در جدول 10-4-5 است
پ) زمانی که سطح کار مرطوب یا در معرض بارش باران و برف است.
ت) زمانی که محل جوشکاری در معرض وزش باد با سرعت بیش از 10 کیلومتر بر ساعت است.
ث) زمانی که پرسنل جوشکاری تحت شرایط غیرایمن و نامتعادل هستند.
2-3-4-4-10 آمادهسازی فلز پایه
سطحی که فلز جوش روی آن رسوب میکند، باید صاف، یکنواخت و عاری از هرگونه پوسته، ترک، زائده و هرگونه ناپیوستگی که اثر سوء بر کیفیت یا مقاومت جوش میگذارد، باشد. سطوحی که باید جوش شوند و سطوح مجاور نوار جوش، باید عاری از هرگونه فلس ضخیم یا شل، گل جوشکاری، رنگ، زنگ، رطوبت، چربی و سایر مواد که از اجرای صحیح و کامل جوش جلوگیری کرده و باعث بخارهای مضر میگردد، باشند. فلسی که با برس سیمی نیز زدوده نمیشود، پوشش خاص نازک ضدزنگ تا 30 میکرون و مواد ضد پاشیدگی جوش میتوانند در جای خود باقی بمانند. در اعضای سازهای که تحت بار دینامیکی قرار دارند، فلس موجود در ناحیه نوار جوش که با جوش قوسی زیر پودری یا جوش قوسی با الکترود روکشدار کم هیدروژن انجام میشود، باید برداشته شود. زخمها و گود افتادگیهای اتفاقی و پراکنده را میتوان با اجازه بازرس، با جوش تعمیر نمود.
مراحل تعمیر باید به شرح زیر باشد:
1- آمادهسازی منطقه تعمیر به طور مناسب
2- جوشکاری با استفاده از الکترود کم هیدروژن
3- سنگ زدن محل تعمیر به طوری که سطح آن صاف شده و همتراز با سطوح مجاور گردد.
3-3-4-4-10 خال جوشها
به استثنای موارد ذکر شده در زیر، خال جوشها باید با همان ضوابط کیفیتی جوش اصلی اجرا شوند:
1- برای خال جوشهایی که در نوار جوش اصلی ذوب میشوند، پیش گرمایش اجباری نیست.
2- ناپیوستگیها نظیر؛ بریدگی لبه جوش، چاله انتهای جوش و تخلخل، لازم نیست قبل از نوار جوش نهایی، تعمیر گردند.
خال جوشهایی که جزئی از جوش اصلی هستند، باید با الکترودی که شرایط جوش اصلی را تأمین مینماید، جوش گردند. خال جوشهای چند عبوره باید دارای انتهای پلهای باشند. به استثنای سازههای تحت بار استاتیکی، خال جوشهایی که جزئی از جوش اصلی نیستند، باید برداشته شوند. در در سازههای تحت بار استاتیکی نیازی به حذف خال جوشها نیست، مگر اینکه بازرس این کار را الزام نماید.
4-3-4-4-10 تعمیر
برای برداشتن مصالح اضافی جوش یا قسمتی از مصالح پایه میتوان از تراشکاری، سنگ زنی، لبه زنی یا شیارزنی استفاده نمود. اعمال مذکور نباید باعث کاهش ضخامت در فلز یا جوش مجاور شوند. در فولادهای اصلاح شده شیار زنی توسط برش هواگاز مجاز نیست. در هنگام برداشتن جوشهای مردود (غیرقابل پذیرش)، مقادیر برداشته شده از فلز پایه باید در حداقل ممکن حفظ گردد. قبل از جوشکاری محل تعمیری، باید سطح شیار ایجادشده کاملاً پاک شود. در جوشکاری تعمیری، کلیه کاهش ضخامتهای ایجادشده در محل سنگ زده شده، باید کاملاً پر شوند. سازنده میتواند جوش مردود را تعمیر نماید یا تمام آن را برداشته و مجدداً به طور کامل جوش دهد، مگر اینکه در مشخصات خصوصی کار به نحو دیگری مشخص شده باشد. معیار پذیرش جوش تعمیر شده، مطابق جوشهای اصلی بوده و با همان روش باید مورد آزمایش قرار گیرد. اگر سازنده تصمیم به تعمیر جوش بگیرد، روش کار به شرح زیر است:
الف) لوچه (بیرون زدگی)، تحدب بیش از حد: مصالح جوش اضافی باید به روش مناسبی برداشته شود.
ب) تقعر بیش از حد حوضچه انتهایی، کمبود در اندازه جوش، بریدگی پای جوش: سطح جوش باید آمادهسازی شده و سپس با انجام عبورهای متوالی، کمبود ضخامتها جبران شود.
ب) امتزاج ناقص، تخلخل بیش از حد، نفوذ گل: مناطق مشکوک باید برداشته شده و جوش گردد.
ت) ترک در جوش یا فلز پایه: در این حالت عمق نفوذ ترک باید به کمک آزمایشهای مناسب (ذرات مغناطیسی، رنگ نافذ، فراصوت و سایر روشهای مؤثر) تعیین شده و تا 50 میلیمتر فراتر از ریشه ترک، مصالح باید کاملاً برداشته شده و مجدداً با جوش پر شود.
5-3-4-4-10 پرکردن سوراخهای اضافی با جوش
بر حسب مورد و طبق نظر مهندس طراح، سوراخهای اشتباه ایجادشده توسط منگنه کردن و مته را میتوان به صورت باز رها نمود یا آنها را توسط پیچ یا جوش پر کرد. در صورت تصمیم به پر کردن سوراخهای اشتباه با جوش، باید موارد زیر مراعات گردد:
(1) درصورتی که فلز پایه تحت تنشهای کششی دینامیکی قرار نداشته باشد، آنها را میتوان با جوش پر نمود، مشروط بر اینکه سازنده برای اجرای جوش از مشخصات فنی مربوط به تعمیرات جوش تبعیت نماید. سلامت جوش باید به کمک یکی از روشهای غیرمخرب، به تأیید برسد. معیارهای پذیرش چنین جوشی در حد جوشهای شیاری است.
(2) درصورتی که فلز پایه تحت تنشهای کششی دینامیکی قرار داشته باشد، میتوان سوراخ را توسط جوش پر نمود، مشروط بر اینکه اولاً نماینده کارفرما تعمیر با جوش و دستور العمل جوشکاری را تأیید کرده باشد، ثانیاً سلامت جوش با استفاده از روشهای غیرمخرب و در رده پذیرش جوشهای شیاری کششی به تأیید برسد.
6-3-4-4-10 پیش گرمایش و حرارت عبورهای میانی
به منظور جلوگیری از وقوع ترک، مقدار پیش گرمایش و حرارت عبورهای میانی باید کافی باشد. حداقل دماهای مقررشده در جدول 10-4-5 در اکثر حالات برای جلوگیری از وقوع ترک کافی هستند. لیکن در وضعیتهایی شامل گیرداری زیاد، هیدروژن زیاد، حرارت القایی جوشکاری کم و قرار گرفتن ترکیبات فولاد در شرایط حداکثری مشخصات فنی، لازم است دمای پیش گرمایش افزایش یابد و بالعکس در شرایط معکوس حالات فوق، میتوان دمای پیش گرمایش را کاهش داد.
جدول 10-4-5: حداقل پیش گرمایش و درجه حرارت عبورهای میانی
مشخصات ورق | روش جوشکاری | نوع فولاد | طبقه | |
حداقل درجۀ حرارت ورق (سانتی گراد) | ضخامت ورق (میلیمتر) | |||
20
65 110 150 |
20≥
20<t≤40 40<t≤65 t>65 |
جوش دستی با الکترود روکشدار (غیراز الکترودهای کم هیدروژن)
|
St37
St52 |
A |
10
20 65 110 |
20≥
20<t≤40 40<t≤65 t>65 |
جوش دستی با الکترود روکشدار کم هیدروژن
جوش زیر پودری جوش تحت حفاظ گاز (الکترود فلزی یا تنگستن) جوش با الکترود توپودری |
St37
St52 |
B |
10
65 110 150 |
20≥
20<t≤40 40<t≤65 t>65 |
جوش دستی با الکترود روکشدار کم هیدروژن
جوش زیر پودری جوش تحت حفاظ گاز (الکترود فلزی یا تنگستن) جوش با الکترود توپودری |
Fy≥400 MPa | C |
1- در جوشکاری ورقها با ضخامت بزرگتر از 25 میلیمتر که تحت بارهای دینامیکی قرار دارند، فقط باید از الکترودهای کم هیدروژن استفاده نمود.
2- هرقدر گیرداری قطعه مورد جوش بیشتر باشد، دمای پیش گرمایش باید افزایش یابد.
3- دمای پیش گرمایش لازم نیست از 230 درجه سلسیوس بیشتر باشد.
7-3-4-4-10 دستورالعمل رویه جوشکاری (WPS)
دستورالعمل رویه جوشکاری باید حاوی کلیه اطلاعات لازم جهت آمادهسازی درز جوش، روش جوشکاری و سایر ویژگیهای مؤثر در مشخصات جوش باشد. دستورالعمل جوشکاری باید طبق فرم استاندارد آن تهیه و به تأیید نماینده کارفرما برسد.
1-7-3-4-4-10 دستورالعمل جوشکاری پیش تأییدشده
دستورالعملهای جوشکاری که از همه لحاظ منطبق بر ضوابط آییننامه جوشکاری ایران (نشریه 228) باشند، میتوانند به عنوان پیش تأییدشده فرض شوند. این جوشها را میتوان از آزمایشهای ارزیابی معاف کرد. در هر حالت مشخصات فنی خصوصی به منظور حصول اطمینان از سلامت و کیفیت جوش، میتواند آزمایش ارزیابی دستورالعمل جوشکاری را الزام نماید.
2-7-3-4-4-10 متغیرهای پایه در دستورالعمل جوشکاری پیش تأییدشده
دستورالعمل جوشکاری پیش تأییدشده باید توسط سازنده به صورت کتبی تهیه شده و برای مراجعه در دسترس باشند. دستورالعملهای جوشکاری پیش تأیید شده میتواند مطابق فرمت آییننامه جوشکاری تهیه گردد، لیکن درج اطلاعات زیر در آن الزامی است:
1- شدت جریان (آمپراژ)
2- اختلاف پتانسیل (ولتاژ)
3- سرعت حرکت الکترود
4- دبی گاز محافظ
5- نوع الکترود
6- دمای پیش گرمایش
7- وضعیت جوشکاری
8- نوع بازرسی
تغییر در هر یک از پارامترهای فوق باید با تأیید نماینده کارفرما امکانپذیر بوده و در صورت تغییر، نیاز به تدوین دستورالعمل جوشکاری جدید است. همچنین میتوان از ترکیبی از دستورالعملهای پیش تأییدشده و نشده در کار استفاده نمود، مشروط بر اینکه محدودیتهای اساسی هر دو دستورالعمل موردتوجه قرار گیرد.
[7] نشریة 228 دفتر امور فنی و تدوین معیارهای سازمان مدیریت و برنامهریزی کشور
[8] Ultrasonic testing rejection rate